Understanding the Basics and Applications of Plastic Extrusion in Modern Production
In the realm of modern-day manufacturing, the method of plastic extrusion plays a crucial role - plastic extrusion. This complex procedure, involving the melting and shaping of plastic through specialized passes away, is leveraged throughout various industries for the development of varied products. From automobile parts to customer products product packaging, the applications are substantial, and the potential for sustainability is equally excellent. Untangling the fundamentals of this process reveals the true adaptability and possibility of plastic extrusion.
The Basics of Plastic Extrusion Process
While it may appear complicated, the basics of the plastic extrusion procedure are based on relatively uncomplicated principles. It is a production process where plastic is thawed and after that shaped right into a continual profile via a die. The plastic extrusion process is thoroughly made use of in various markets due to its adaptability, performance, and cost-effectiveness.
Different Kinds Of Plastic Extrusion Strategies
Structure upon the basic understanding of the plastic extrusion process, it is necessary to discover the numerous methods included in this manufacturing method. The 2 main techniques are profile extrusion and sheet extrusion. In profile extrusion, plastic is thawed and developed into a continual account, often made use of to produce pipes, poles, rails, and window frames. In contrast, sheet extrusion develops big, flat sheets of plastic, which are usually further refined right into products such as food product packaging, shower curtains, and vehicle components. Each method requires specialized equipment and accurate control over temperature level and pressure to ensure the plastic keeps its shape throughout cooling. Understanding these strategies is key to making use of plastic extrusion successfully in modern manufacturing.
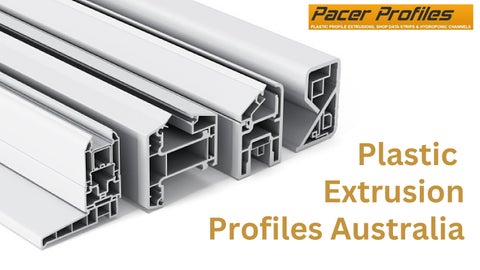
The Function of Plastic Extrusion in the Automotive Industry
An overwhelming majority of components in modern-day vehicles are products of the plastic extrusion process. Plastic extrusion is mostly made use of in the production of different auto components such as bumpers, grills, door panels, and control panel trim. Thus, plastic extrusion plays an essential duty in automotive manufacturing.

Applications of Plastic Extrusion in Consumer Item Production
Beyond its substantial effect on the automobile sector, plastic extrusion proves equally reliable in the world of customer products manufacturing. This procedure is vital in creating a large array of items, from food packaging to family appliances, playthings, and even medical gadgets. The flexibility of plastic extrusion permits producers to make and create intricate sizes and shapes with high precision and effectiveness. Moreover, because of the recyclability of many plastics, extruded parts can be reprocessed, minimizing waste and price. The flexibility, versatility, and cost-effectiveness of plastic extrusion make it a recommended choice for numerous durable goods manufacturers, contributing significantly to the market's development and advancement. The environmental implications of this extensive use need cautious factor to consider, a subject to be gone over additionally in the succeeding area.
Environmental Influence and Sustainability in Plastic Extrusion
The prevalent use plastic extrusion in manufacturing welcomes examination of its ecological ramifications. As a process that frequently makes use of non-biodegradable materials, the ecological effect can be considerable. Power usage, waste manufacturing, and carbon discharges are all issues. Nonetheless, market advancements are raising sustainability. Efficient equipment reduces power use, while waste administration systems recycle scrap plastic, reducing raw product demands. Furthermore, the growth of biodegradable plastics supplies a more eco-friendly option. Despite these enhancements, further advancement is required to reduce the environmental impact of plastic extrusion. As society click here for more info leans in the direction of sustainability, manufacturers need to adjust to remain practical, stressing the importance of constant research study and advancement in this field.
Verdict
In verdict, plastic extrusion plays a critical function in modern production, specifically in the automotive and customer products fields. Comprehending the basics of this procedure is key to enhancing its advantages and applications.

The plastic extrusion process is extensively used in various industries due to its cost-effectiveness, performance, and convenience.
Building upon the standard understanding of the plastic extrusion process, it is required plastic extrusion to explore the numerous methods involved in this production technique. plastic extrusion. In contrast, recommended you read sheet extrusion develops big, flat sheets of plastic, which are typically more refined into items such as food packaging, shower drapes, and cars and truck parts.A frustrating majority of components in contemporary vehicles are items of the plastic extrusion process